Farm Management
Growers should consider and investigate many factors in the broiler industry before building a commercial poultry farm—type of farm, revenues and expenses, required capital, insurance, startup costs, farm loans, and even lifestyle. Learn more in this fourth of a five-part series for new farmers in the commercial broiler industry.
Estimating Expenses & Net Income of a New Poultry Farm
A commercial poultry farm’s operating expenses across farm types are often estimated at 30 to 35 percent of gross revenue. A farm loan payment accounting for another half of the revenue leaves only 15 to 20 percent of revenue as net farm income. Often the only way to increase this return is by directly reducing variable inputs such as fuel or electricity.
The good news is that housing technologies and building techniques in the last decade have lowered the operational expenses of newer farms closer to 25 percent of gross revenue and have proven to retain these efficiencies longer.
Many growers are now building larger, more efficient houses with more houses per farm to capture greater economies of scale and the best returns. The downside to this trend is that the increased capital, labor, and management needed to build and operate these large farms can be limiting.
The typical poultry farm loan has a 15-year term. However, twenty-year loans are becoming more prevalent as growers look to improve cash flow and sustain net revenue. This can cause a less-than- desirable equity position during the later years of the loan, making it more challenging to secure refinancing for the maintenance and equipment replacement often required to support ongoing operations.
Financial Analysis
Integrators typically have business cash flow estimates pertaining to the three live production sectors. These pro forma documents should be based on the production expectations of the local complex and reflect a reasonable estimate of expenses for the area.
These numbers are almost always restricted to each sector’s average income and costs over time. Both income and costs can vary outside of these average numbers, sometimes significantly, causing short- term strains in cash flow that can turn into long-term problems.
A proper financial analysis of the business should include the impacts of short-term income restrictions, cost escalations, or both. These can be grower and integrator related. Scenarios include disease-caused flock interruptions, market changes causing extended out times, or weather-related disruptions.
As a potential grower, you need to know how these can affect your cash flow, how well the business can financially handle such disruptions, and for how long. Discuss these and similar scenarios with a lender with poultry loan experience to better understand ways to prepare for such inevitable occurrences. Discuss with the integrator possible variances in pay based on performance. For more financial information, see New Farmer’s Guide to the Commercial Broiler Industry: Purchasing an Existing Farm, ANR-2940.
Lifestyle Considerations
Since commercial poultry operations require a significant amount of labor and daily management, the business’s long-term success is closely related to a grower’s and family’s satisfaction with the farm’s lifestyle. This is somewhat difficult to predict until you are in the business.
Talk to as many growers of various-sized farms as possible to better understand what daily life will be like on the farm. Talk to growers with similar housing and birds to those you are considering, especially growers working for the same integrator as you will be, to get a cross-sectional view of the business. A good understanding of a poultry farm’s potential ups and downs is important before entering this business.
If you have little to no knowledge of the poultry business, contact a grower and ask permission to visit a farm. Even better, ask if you can spend time working with a grower, performing daily tasks, to gain a firm understanding of what is needed to be successful.
Most integrators require contract growers or their hired managers to live on the farm property or within a defined distance from the farm. The cost of accommodations on the farm should be calculated into the overall business plan. One question to ask an existing grower is, What is it like to live on the farm?
Consider future quality-of-life costs and decide if the projected farm income can support expectations in this area. Long-term success also requires a certain amount of financial discipline. You must ask your family and yourself if these requirements can be met. Living outside the lifestyle the farm supplies is often a cause of failure by a poultry farm business.
The contract poultry farm is considered to have an overall lower risk from market changes compared to many other farming businesses, but it does not come with zero risk. Understanding what risks exist can help you make better business decisions. As with any business, lower risk often comes with lower potential returns on investment.
Next Steps
Moving from a general overview into taking steps to pursue a business should include the guidance of a local broiler company representative. Contact the local poultry company’s live production office to inquire if there are any opportunities for new growers in the desired farm type. There may be an immediate need for additional housing or a waiting list of potential future growers.
It can be argued that this is the first step to take. If local companies do not currently have room for more growers, there is no opportunity to explore building a new farm. Either way, the company can offer direction and will have other questions and requirements to consider.
Location Considerations
The first aspect of starting a new poultry farm is to examine the physical location. The new farm must be inside the zone of operations for the local broiler complex. Usually, this is a locally determined radius from the complex feed mill or main operations center. If a prospective location falls within these limits, the next question is more complicated: Is the land suitable for the desired farm type and size?
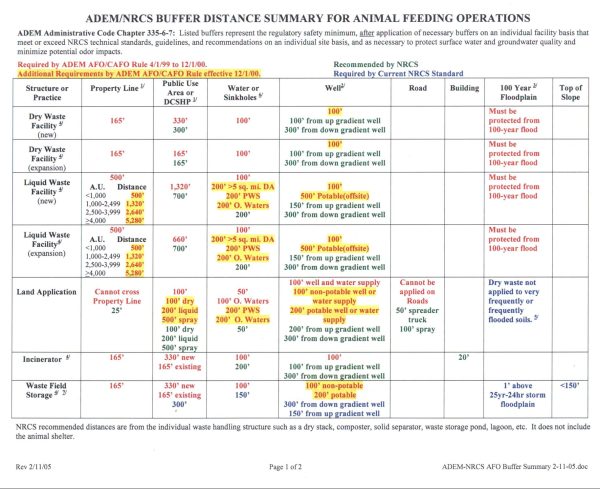
Example of a regulatory agency’s farm location guide sheet. All farm structures must meet the requirements set forth by governing agencies such as the EPA, NRCS, and possibly additional local or state regulations. This is just an example, please check with your local agencies for specific guidance in your area.
Federal, state, and local governments have regulations that can affect the physical location of animal feeding operations. Regulations can vary widely with state and local governments. These can include zoning laws that prohibit new housing in some areas or restrict the type and overall size of the operation.
If there are no overarching restrictions to a farm’s existence on the property, there will be state regulations for the facility’s proximity to property lines, other public facilities, neighboring residences, riparian water sources, wells, etc. The projected facilities must fit within these guidelines. There also will be regulations on waste removal, storage, and handling that could impact whether a piece of land is suitable for a new facility.
Contact the offices of the local Farm Services Agency and Natural Resource Conservation Service (NRCS) for answers to these questions. Sometimes the company’s live production office will have some of this information already prepared. The local NRCS office will eventually form the farm’s waste management plan. The integrator will likely take soil samples to check for the presence of pesticides or contaminants that could pose a threat to food safety.
The prospective property will need access to utility services and sufficient water sources, either wells or municipal water, or both. New farms often require two water sources or multiple wells, and the water quality must meet husbandry standards. The integrator dictates the minimum requirements for each according to farm size. All costs of supplying utilities fall upon the grower. More remote properties may incur higher than normal utility access costs.
When considering the placement of a new farm facility, it is wise to consider the good-neighbor policy. Sometimes a proposed facility meets all the regulatory requirements of the state and local government, but other factors could prove problematic in the future.
Talk to potential neighbors about your proposal to learn how they feel about the new farm. It may be beneficial to orient the facility to minimize potential nuisances, even if it costs a little more. In these cases, the long-term benefit for the farmer and the industry far outweighs the increased cost.
At the extreme, some properties are just not suited for a new facility based on this good-neighbor policy alone. For instance, if a potential farm is to be built next to a piece of land recently sold to a land developer with plans to build a residential subdivision, the potential for future conflict could render the property unsuitable for a new farm.
Poultry Housing Specifications

Every new poultry house should be constructed to meet a professionally engineered design like the example shown here. The design should be specific for the farm location, considering local weather and soil conditions, stamped and signed by an engineer accredited in the state.
The local poultry company office has housing specifications for every type of new live production facility in their complex. These should be part of a package of documents received from the live production office. These specifications may include guidance on location requirements that go beyond local governmental requirements. They will have guidance on what type and size houses are to be built and equipment requirements.
Structural specifications should include professionally engineered design drawings for the structures specific to the general area, considering local soil types and weather patterns. Once the housing number and size are decided, a general layout of a farm in total, including all outbuildings and access roads should be produced. This layout will aid you in placing the farm on the chosen property to meet all required property line setbacks
and restrictions.
Housing specifications can be highly detailed or more general, but they should be sufficiently detailed to take to a poultry builder for bidding a new facility. The grower’s responsibility is to ensure that the builder bids and delivers a facility that meets the company’s requirements. Therefore, the more detailed the specifications, or the closer the guidance of the company, the better the quality of build to be expected.
Additional Capital Considerations
Every poultry operation requires rolling equipment to operate. Tractors, trailers, litter-handling equipment, and the like, are all expenses associated with starting a farm. These capital needs must be considered whether they are added as new assets or shared with another enterprise on the farm.
Additional outbuildings also must be considered. Litter sheds and mortality handling facilities are important parts of the operation that must be part of the business plan. Contact the local NRCS office for cost-share opportunities in waste management structures and equipment and for mortality disposal facilities.
Insurance
Insurance coverage is critical for any poultry farming operation and is required before a lender finalizes a loan. Insurance coverage for commercial poultry farms is becoming difficult to secure in some areas, and the cost can be prohibitive. It is advisable to contact potential insurance carriers early in the purchasing process.
A builder’s risk policy is typically required to be in place during the construction phase. Insurance companies often want to inspect the facility as it is being constructed and may have specific structural or equipment requirements beyond basic housing specifications.
Additional types of coverages should be discussed, such as loss of income or business interruption coverage, equipment mechanical failure coverage, and replacement cost value versus depreciated cash value- only coverage for property damages.
Of these coverages, loss of income or business interruption coverage must be carefully evaluated. Most policies will replace all or most income lost directly to a covered peril. For instance, if a fire destroys a house, insurance typically covers a portion of the income that would have come from the lost flock of birds. However, policy limits may prevent payment for all the income lost during the reconstruction phase. It is recommended that a policy have loss of income coverage with limits equal to or exceeding 6 months of normal net revenue to allow for farm repair while not imposing financial hardship.
Start-Up Costs
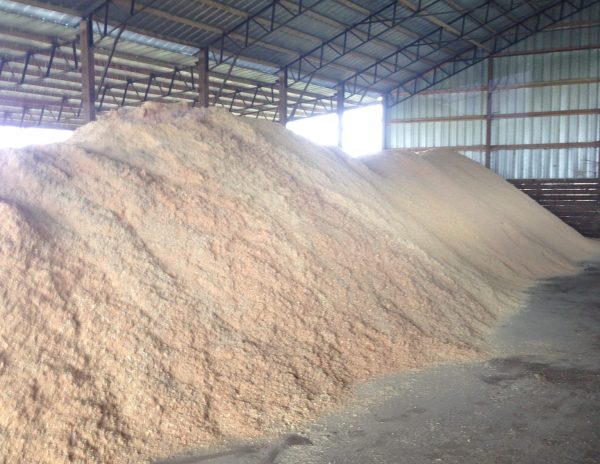
Every new farm will have start-up costs, and every existing farm will have new flock set-up costs. Having working capital available to cover such things as this semi-truckload of new shavings for litter is important for both new growers and established farms.
Every new farm will have additional start-up costs. These can include recurring flock inputs, such as litter, chick feed trays, diesel fuel for generators and rolling equipment, litter ammonia treatments, litter beetle pesticide, and sanitation products. In addition, the farmer must account for utility deposits and hookup fees, monthly utility bills due before flock payment, and weekly labor expenses.
The start a business, the capital to cover these expenses must be at hand. Too often, new growers are unprepared for these expenses and quickly find themselves deep in credit card debt or encumbered with other high-interest, short-term loans. Having substantial working cash on hand is always the best option. However, adding a percentage of these expenses into the farm loan upfront can be a viable option that will cost less than using unsecured debt as a capital source.
The amount of working capital needed varies with farm type and size. Location and season also can impact immediate working capital needs in the form of heating fuel or electricity requirements. If these bills come due before a flock settlement takes place, working capital must be at hand to cover them.
It is a good practice to budget ahead for flock expenses that will be due before flock payments arrive and to continue the practice even after the farm begins receiving flock payments. For broiler farms in general, one quarter (25 percent) of a farm’s annual variable expenses should be available for working capital. With pullet and breeder farms, which are paid biweekly or weekly, working capital needs are lower but still must be considered. Once a farm is up and running and revenue is coming in, proper budgeting should include establishing sufficient working capital to carry the farm through for several months.
Business Entity Choice and Financing
A commercial poultry farm is a large agribusiness entity. Careful consideration is needed as to the kind of business entity chosen, as it has direct impact on income taxes, business liability issues, and future farm succession. The business structure chosen, whether a limited liability company, a sole proprietorship, or other, can have a significant impact on how the business fits into the household income-tax structure.
One of the first steps to take in moving forward on a new farm build is to contact a competent accountant and attorney skilled in a new business setup. It is especially helpful if they have experience with agricultural businesses.
Building a new poultry facility is expensive and proper financing is imperative. The best place to start a loan discussion is with a specialized agriculture lender. Agriculture lenders understand the business model and can guide you through the processes. They are often local, giving them knowledge of the poultry business in the area. Agriculture lenders are usually skilled in navigating government farm loan guarantees or subsidies and integrating multiple farm enterprises into a financial loan package.
Consider talking to more than one lender to compare products and procedures to find one that best fits your goals.
Additional Resources
- “Evaluating Water Quality for Poultry” on the Alabama Extension website at www.aces.edu.
- “Nutrient Management Planning for Broiler AFOs” on the Alabama Extension website at www.aces.edu.
- “Mortality Disposal Methods for Commercial Poultry Growers” and “Construction of a Dead-Poultry Composter” on the Alabama Extension website at www.aces.edu.
- “New Farmer’s Guide to the Commercial Broiler Industry: Business and Financing” on the Alabama Extension website at www.aces.edu.
Back to New Farmer’s Guide to the Commercial Broiler Industry
Dennis Brothers, Associate Extension Professor, Agricultural Economics and Rural Sociology, Auburn University
New October 2022, New Farmer’s Guide to the Commercial Broiler Industry: Building a New Farm, ANR-2941