Commercial Poultry
Conduct a poultry house wind speed maintenance check in the spring before hot weather arrives. The goal is to achieve maximum full tunnel wind speed and evaporative cooling performance, exceed minimum wind speed requirements with ease, and help prevent emergency repairs during hot weather operation.
Tunnel Fan Maintenance Checklist
Tunnel fans are the lifeblood of tunnel windchill cooling and bird cooling is drastically needed during hot weather. All tunnel fans must be in top shape before they are needed. Insufficient fan maintenance often results in insufficient wind speed and reduces hot weather performance. Following is a maintenance checklist:
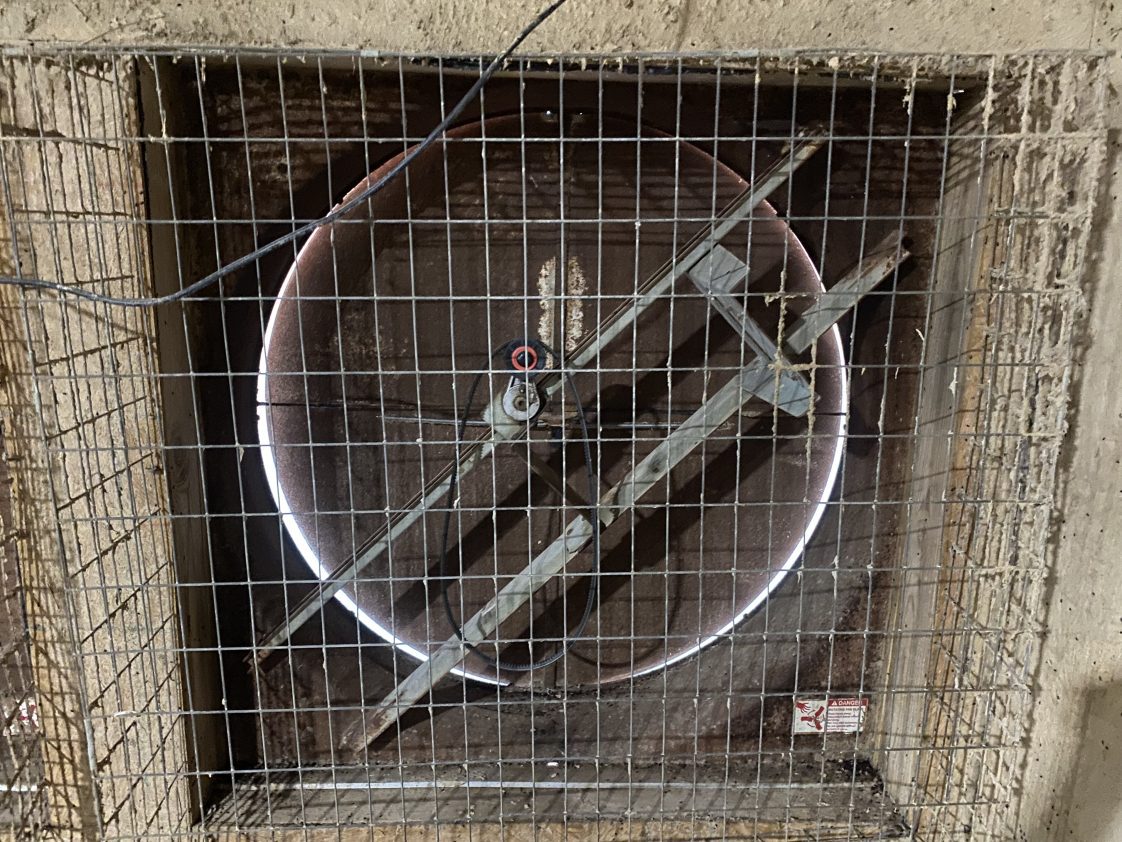
Figure 1. Can you identify the problem with the fan in this picture? A. No motor, B. No propeller, C. Not clean, D. All the above. If you answered, D (All the above), you would be correct. Also note that the adjacent tunnel fan #3 is plugged into the outlet above this fan, tunnel fan #1. This fan is not ready for hot weather.
1. Drives (Pulleys and Belts). The drives transmit power and provide the gear ratio between motor and propeller speed. Anything that goes wrong with the drive system causes lost fan performance. Check belt tension: loose belts reduce the gear ratio, causing airflow loss and reducing belt life. Check belts for wear: belts riding lower in the pulleys change the gear ratio and lower fan performance. Check pulley alignment: misaligned pulleys cause excessive belt wear and more drive losses. Check pulleys for wear: cupped-out pulleys allow belts (even a new belt) to ride lower in the pulley, which changes gear ratio and lowers airflow.
2. Tensioners. Fan tensioners must deliver full tension on the fan belt for the fan to operate at the maximum designed potential. These must be lubricated, exercised by hand, and inspected closely to make sure that they align with the prop and motor pulleys. Make sure the dry bearing on this pulley is not damaged and causing unnecessary drag on the fan belt and motor. One or two bad tensioners can keep a house from reaching full wind speed potential. In most cases, damaged tensioners simply need to be replaced with a new one to regain like-new fan performance.
3. Shutters and Guards. Anything that obstructs the airflow causes lost fan performance. Clean shutters once per week during tunnel ventilation. Dirty shutters require more energy from the airflow to open, and they reduce airflow and efficiency. Clean guards once a week because dirty guards present more surface area to obstruct airflow. All butterfly shutters or dampers must be in perfect working condition. If they do not fully open and close, they will create a problem with house tightness. Significant ventilation problems can be the result of damaged butterfly shutters.
4. Motors. Most electric circuits and electrical devices run more efficiently and last longer at cooler temperatures. Dirty motors run hotter, lose efficiency, and have reduced motor life. Clean motors once per flock. Have at least one motor already wired and a pulley installed for a quick motor swap when needed.
5. Bearings. Lubricate bearings twice per year where applicable (spring and fall). Dry bearings require more power to turn, reduce fan efficiency, and shorten bearing life. Bring new grease fittings with you when you start greasing because one or two will often not take grease and will need to be replaced.
6. Power Cords. Make sure all power cords are in good operating condition and that the power outlets, if applicable, are not loose, charred, or damaged in anyway. Eliminate human safety hazards, fire hazards, and fan failures from happening when fans are called to run continuously.
Evaporative Cooling Checklist
Time and effort spent maintaining the evaporative cooling system not only improve the cooling performance of the house but they also extend the life of the evaporative pads and pumps. Following are more tips:
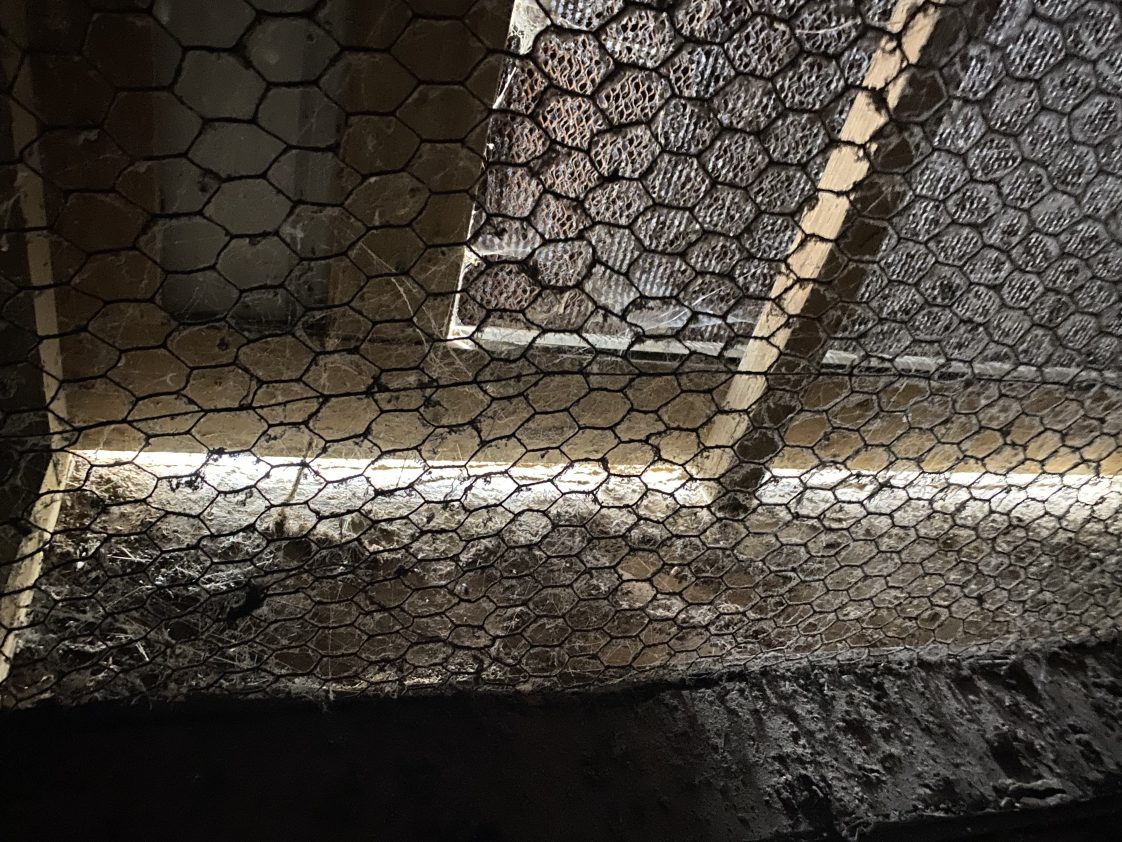
Figure 2. Can you identify the problem or problems in this picture taken from the inside of a broiler house looking through the tunnel inlet? A. Cobwebs on pads, B. Cobwebs on bird wire of inlet, C. Light and air leak entering between the floor and wall of the doghouse, D. Floor is dirty, E. All the above. If you answered, E. (All the above), you would be correct. This doghouse and pad system are not ready for hot weather.
1. Pads. Blow debris from inside or outside of pad system to doghouse with backpack blower with pads dry. Then thoroughly clean and rinse the system.Excessively dirty pads are often the result of poor wind speed and high static pressure. If pads are damaged or cannot be adequately cleaned, they must be replaced to restore the house to like-new airflow and wind speed potential.
2. Doghouse. Sweep all cobwebs and other debris from the back of the pads with a broom or blow out with a blower. Once everything is on the floor, remove it from the doghouse. Then do a thorough inspection for any air leaks that might be present. Check along the ceiling, floors, and evaporative system for places air can bypass wet pads. Spray foaming air leaks isa quick and simple method to fill cracks, but is not usually a permanent fix.
3. Filters. Remove and clean or replace filters.Replacement filters must be stored on site and be readily available when needed. Inspect filters once a week during high-use times. Do not operate a system without filters or screens in place.
4. Pumps, Floats, and Tanks. Make sure pump intake screens are clean and floats are in place and adjusted. Tanks must be clean and free from debris.Inspect pump screens at least once a week during high-use periods or as often as the system is drained and flushed.
5. Distribution Header. Flush the distribution header.Loosen the union at the distribution header and carefully clean all distribution holes with a screwdriver or soft-bristle brush. Do not change the size of the hole in the header. Run water in the system to ensure that all holes are free from debris or clogs.
6. Water Supply. Test run recirculation system to make sure that the water fill levels are adjusted properly and adequate water is available to fill system.Make sure the supply system fully wets the entire pad system and with no dry streaks on the pads. If water quality problems surface, additional filtration or treatment may be necessary. One simple way to extend system life is to routinely flush the water during high use. One system flush per week is much better than once per flock or per year.
7. Tunnel Inlet Opening. The inlet curtain opening must be at least 80 percent of the cooling pad system area. For example, for 1,000 square feet of 6-inch recirculating pad, there must be a minimum of 800square feet of free air unobstructed inlet opening. Bunched up curtains or partially opened tunnel doors must not restrict the tunnel inlet opening. This is an ideal time to test run the tunnel inlet for proper operation. Broken strings, damaged pulleys, holes in the curtains, and twisted cables keep inlets from functioning properly.
Tunnel House Tightness Checklist
Minimize all possible air leaks that will take away from the full house wind speed potential. Spring is an ideal time to conduct a house tightness test per company guidelines to make sure houses are sealed for efficient environmental control. Record and document for future reference and repeatability this test result and the fan or fans used in the control room of each house.
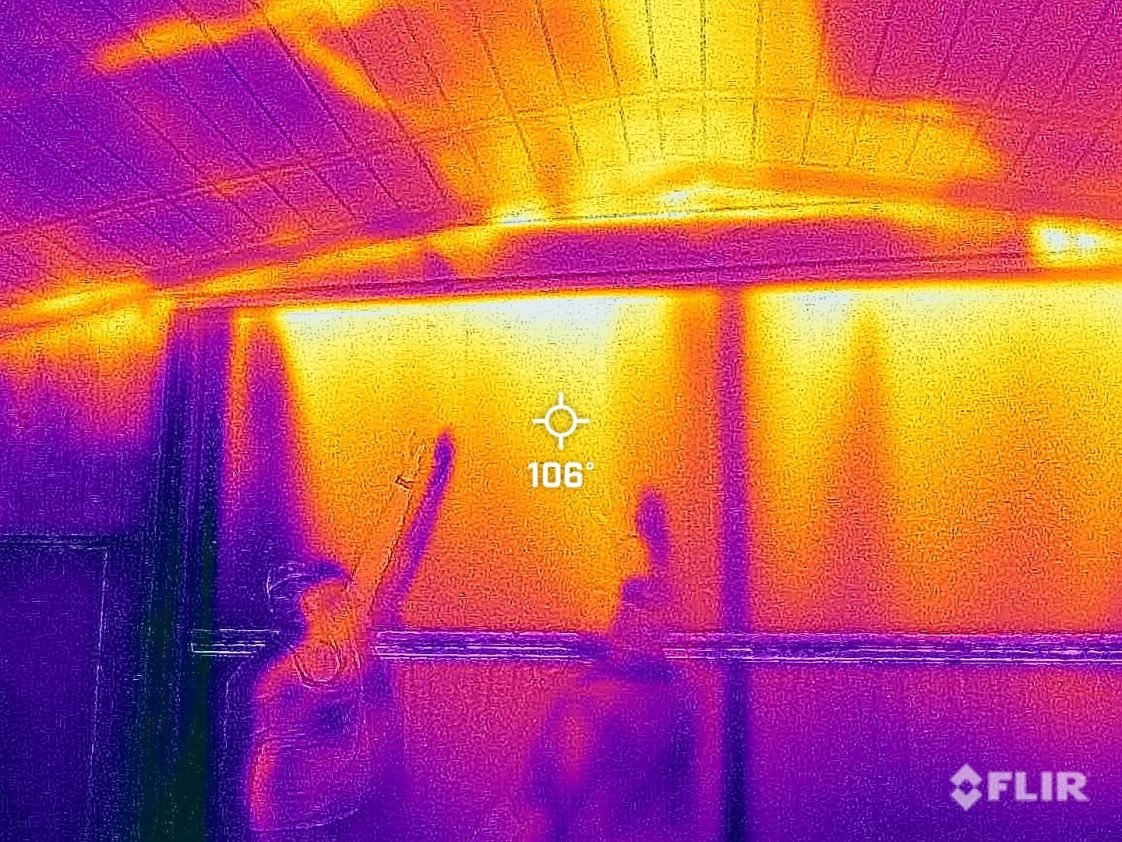
Figure 3. Can you identify the problem or problems in this thermal image of an end wall door? A. Top of door leaking hot air, B. No insulation in ceiling, C. Air leaking between ceiling and end wall, D. Hot air leaking through these openings would lower full tunnel wind speed and lead to additional heat gain from missing insulation, E. All the above. If you answered E (All the above), you would be correct. Once again, this house is not ready for hot weather and might not pass a house tightness test or wind speed test.
1. Ceilings. Inspect and seal all attic access boards, doors, and leaks need to keep from leaking attic air into the house. Replace damaged attic inlets or remove and cover with plywood or equivalent.
2. Doors. All end wall doors must be inspected for safe operation and for air leaks. Inspect, seal, and repair as needed.
3. Perimeter Inlets. All sidewall or ceiling inlets need to be inspected for air leaks and proper operation. If the insulation is damaged, repair or replace it. Air leaks are often found around damaged metal vent doors. If left unsealed, these can seriously contribute to air leaks down the house.
4. Foundation. Make sure all sidewall and foundation leaks have been identified and sealed properly. Small foundation leaks added together end up being significant contributors of hot air leaks, and these leaks are often low at the foundation. The hottest place in the house during tunnel ventilation and the lowest wind speed location are typically along the foundations down each sidewall.
5. Curtains. All tunnel houses that have sidewall curtains should have a top curtain flap and bottom lumber strip or equivalent seal at the bottom. Loose curtains can drastically reduce full tunnel wind speed. Holes and tears in curtains must be repaired with curtain tape or an equivalent method that will last.
6. Inlet and Vent Machines. Tunnel inlet and sidewall vent machines and strap machines must be cleaned, inspected, repaired, and serviced just like any other piece of equipment. Grease those gears! Make sure all connections, limits, cables, and straps are in reliable condition and function flawlessly. These machines can sometimes get out of adjustment and need to be recalibrated or reset in the controller to make sure they fully open and close when used.
Bottom Line
Even though this is not a comprehensive maintenance checklist, it can help identify things that may go overlooked when time is short. The goal is full potential wind speed, performance, and prevention of emergency repairs during hot-weather operation. More information about this and other poultry house–related topics are available at www.poultryhouse.com or download the Poultry Toolkit app.
Contact:
Jess Campbell
National Poultry Technology Center at Auburn University
jesscamp@aces.edu
(334) 332-6830
Jess Campbell, Associate Extension Professor; National Poultry Technology Center; Jeremiah Davis, Professor, Director, National Poultry Technology Center; Cody Smith, Research Engineer, Biosystems Engineering; and Kelly Griggs, Research Engineer, Biosystems Engineering, all with the National Poultry Technology Center, Auburn University
New April 2024, Poultry House Spring Wind Speed Maintenance Checklist, ANR-3071