Crop Production
Center pivot irrigation (CPI) is steadily becoming the most popular irrigation technology throughout Alabama and the Southeast. A CPI system is comprised of a pump, a series of lateral pipes that are supported by ground structures called towers, and sprinklers that are installed along the pipeline. The sections of pipeline between the towers are referred to as spans. As more growers have adopted this method of irrigation, many have run into problems with their center pivot systems.
When a CPI system is installed, the manufacturer will provide a sprinkler chart that details the correct nozzle sizes, pump pressure, and flow rate for the system. The most common issues with CPI systems often stem from a mismatch between the prescribed settings in the sprinkler chart and the operational settings used by growers.
Operating with Incorrect Pump Pressure
Sprinkler charts for CPI systems are designed for a specific pumping pressure. The nozzle sizes recommended by the manufacturer are specific to the pressure being used for the system, which makes proper operating pressure crucial.
If the operating pressure is below what is recommended, the water droplet size will be too large. This will decrease water flow throughout the pipeline and will limit water application area in the field. Conversely, if the operating pressure is above the designed pressure, the water droplet size will be too small. These smaller droplets are more prone to evaporation and wind drift, which will decrease the efficiency of irrigation in the field.
The most common causes of pressure errors include the following:
- wells where groundwater levels decline throughout the growing season
- worn pump impellers
- water leaks along the system
- terrain elevation
Any of these causes can lead to insufficient or excessive pressure, which then increases energy costs because of over-application of water. To avoid these problems, growers should frequently check the pump pressure (either manually or automatically) and monitor water source levels (either in a well or a pond) to identify potential problems with pump pressure.
Operating with Incorrect Nozzle Selection
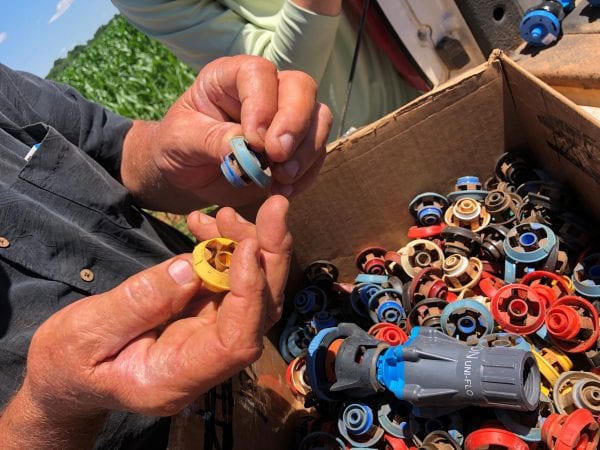
Incorrect nozzle selection might impact irrigation rate. Nozzle color indicates its size and water pressure.
CPI systems apply water from the pipeline to the field using sets of sprinklers along the spans. These sprinklers are designed to use specific nozzle sizes for specific pressures. The effects of incorrect nozzle selection are similar to those of incorrect pump pressure, as both are designed with respect to each other.
If the nozzle openings (orifices) are too small for the operating pressure, water flow is restricted which leads to decreased irrigation application. If nozzle orifices are too large, water will flow at higher rates than intended, which may lead to over-application of water in spans closer to the center pivot and under-application in spans further from the center pivot. To see a specific case study regarding incorrect nozzles sizes, read the Alabama Extension publication Operation & Maintenance Problems of Center Pivot Irrigation, ANR-2772.
As with incorrect pump pressure, these errors have an economic impact as well. Under-application of water, especially in the larger areas covered by the outer spans, can lead to decreased yield at the end of the growing season (see ANR-2772 for more information).
To avoid the negative impacts of incorrect nozzle selection, growers should ensure that all nozzle sizes on their CPI systems match the sizes recommended in the manufacturer’s sprinkler chart. If the nozzle sizes match those on the sprinkler chart but application errors continue, growers should also check to ensure that the operating pressure matches the designed pivot pressure on the sprinkler chart and that the nozzles are not clogged or damaged.
The Importance of Irrigation System Control Panel Settings
In CPI systems, the travel speed of the pivot determines the amount of water applied throughout the field. For every pivot, a chart is provided (often stored at the control panel) that indicates the amount of water applied according to various pivot speeds. In most cases, the speed is set as a percentage, with 100 percent indicating continuous movement for the pivot end tower. Growers can adjust this percentage to fit their needs. For example, a setting at 50 percent would indicate that the pivot end tower will move for 30 seconds and then stop for 30 seconds in a 60-second period.
If the incorrect speed is used, this can lead to over or under-application of water. If the pivot runs too quickly, under-application is likely to occur as not enough time is allowed for water to be applied. If the pivot runs too slowly, over-application is likely to occur as water is still being applied in areas that may already be saturated.
The easiest way to catch pivot speed errors is to monitor the amount of time it takes for a CPI system to complete a full revolution. If there is a mismatch between the expected revolution time and the actual revolution time, there is likely an issue on the control panel, be it machine or human error. By catching these problems early in the growing season, economic effects– such as yield loss or increased energy expenses from over-application– can be avoided. If a pivot application chart is not available with the CPI system, growers should contact the manufacturer so that a chart can be provided.