Crop Production
Learn the basics of greenhouse cucumber production, including seeding production; training, pruning, and spacing; the greenhouse environment; fertilization and irrigation; and harvesting and fruit quality.
Cucumbers are a popular crop for greenhouse vegetable production. English and Beit Alpha are the two primary cucumber types grown in greenhouses. Both types are parthenocarpic, meaning they produce fruit without flower fertilization and do not require pollination. Due to the absence of a fertilized ovule in the fruit, these cucumbers have no seeds and are marketed as “seedless.”
Cucumbers are typically tolerant of extreme summer temperatures and are considered a fast crop with the first harvest ready within as little as 7 weeks from seeding. This fast turnover time allows for great flexibility in crop cycles. Cucumbers perform somewhat better than tomatoes in extreme summer temperatures; however, yield can suffer in the winter with low light levels and conservative heating strategies. An ideal crop timing has not yet been established in Alabama; however, research trials show that two crop cycles per year are an efficient model. A spring crop can be seeded in December for January transplanting and harvested from February to July. The harvest interval of a spring crop can extend past 12 weeks, depending on greenhouse temperatures. However, In the southeastern United States, temperatures typically exceed ideal growth conditions by July, and the spring planted crop is removed. For a fall crop, seeds are started in July, transplanted in August, and harvested from September to December.
Seedling Production
Starting cucumbers in flats from seed before transplanting them into the production system saves valuable time and production space in the greenhouse. Seeds can be started in a 50-cell (11′′x22′′) or larger nursery flat using a peat-based potting mix. Irrigate seedlings with plain water until true leaves have emerged, then switch to a half-strength fertilizer solution (50-100 ppm N).
Growing Systems
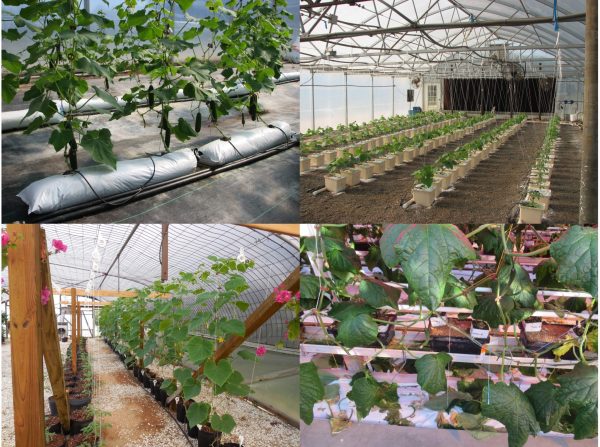
Figure 1. Layflat poly bags filled with perlite (upper left); dutch bucket system filled with perlite (upper right); 3-gallon nursery pots filled with aged pine bark (lower left); and Rockwool seedling blocks used on perlite- filled containers (lower right).
Vine crops such as cucumbers, tomatoes, and peppers are often grown in substrate-based systems. This method differs from true hydroponics (nutrient film technique and deep water culture) in that a soilless substrate is used to support the root system and provide a higher degree of aeration.
Three main types of substrates are used in greenhouse production. Perlite and pine bark are the most common substrates used in the southeast. Perlite is a volcanic rock that has been expanded by heat treatment. It is a lightweight, highly porous inert substance that does not contain or hold nutrients. Pine bark is an organic material that can hold some nutrients. Pine bark is typically milled to 1⁄2 inch and should be aged before use. Rockwool is another substrate used to cultivate crops; it is primarily used in high-wire systems. Rockwool comes in large cubes or slabs and often rests on plastic troughs to drain nutrients. Rockwool seedling blocks are also used for transplant production. These blocks are placed on top of Rockwool slabs or other soilless media. Rockwool is inert like perlite and has a high water- holding capacity.
Several substrate production systems can accommodate cucumber production using the aforementioned substrates (figure 1):
- Dutch bucket: a plastic bucket fitted with a drainage hole in the bottom for nutrient solution to flow out and be reused if desired. Perlite and pine bark can be used in dutch buckets.
- Bag culture: a flexible plastic bag is filled with the desired substrate, and drainage holes are poked on the bag’s underside to allow for water and airflow through the substrate. The bags can be positioned horizontally or vertically under the trellis system. Holes are cut in the top of the bags for transplants. Perlite and pine bark can be used with bags; however, perlite seems the most popular.
- Nursery pots: typically 3- or 5-gallon plastic pots used in the ornamental nursery industry. Both perlite and pine bark substrate can be used with nursery pots.
- Slab culture: a slab made of Rockwool is used to anchor plant roots and hold water.
Training, Pruning, and Spacing
Cucumbers are trained to grow vertically on strings suspended from a wire cable. The trellis system should run parallel with the greenhouse. Advanced greenhouse systems commonly used in northern climates use a high-wire system where crops are grown on strings suspended from trellises with heights over 12 feet (figure 2). This system favors cooler climates in terms of efficiency and has not been thoroughly validated in Alabama. Most greenhouse vegetable operations in the southern states use a similar trellis system, but they are considerably shorter in height (6 to 8 feet) (figure 2).
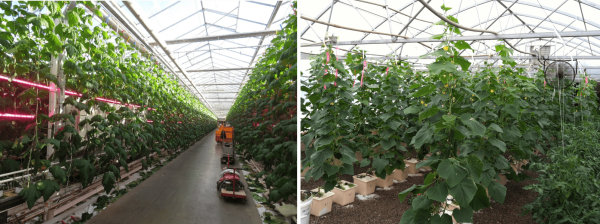
Figure 2. High-wire system in advanced dutch greenhouse (left). Common shorter trellis system used in the southern United States (right).
Growing plants upright takes advantage of the vertical space in the greenhouse and allows for high-density planting. Rows are typically spaced on 5-foot centers. A 30-foot wide greenhouse will support 5 rows.
Plants can be trained and pruned several ways resulting in various plant densities (plants per area). The optimum density isn’t always the highest. In some cases, too many plants can result in lower yields. The optimum density maximizes yields with available light. Plant density might be reduced by 25 percent or more in the winter months to maximize light available to leaves.
The two training methods are the vertical cordon and the v-cordon system. In both systems, flowers are not allowed to form until the sixth or seventh true leaf, allowing a more favorable leaf:fruit ratio. Fruit abortion and malformed fruit are problems when over-fruiting occurs (figure 3).
The vertical cordon arrangement places plants directly under the wire trellis cable, where plants are trained to a single leader. Within the row, plants are spaced 12 to 18 inches (figure 4). The vertical cordon system can also be used with a double row, where two wires are spaced 2 feet apart within the row (figure 5). Rows are spaced 5 feet apart on center, and plants are spaced at slightly larger distances (18 to 24 inches). In the double row system, plants are staggered to maximize light interception.
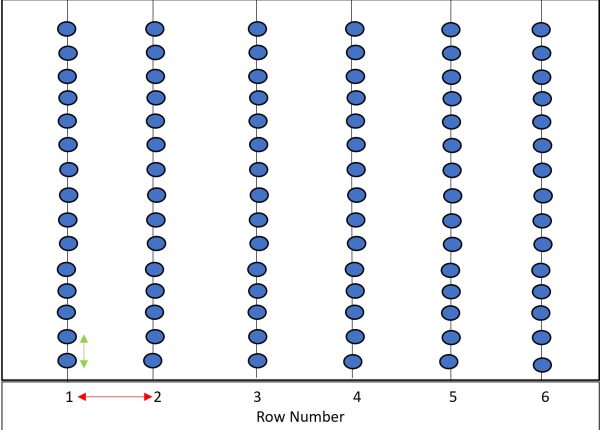
Figure 4. Single-row vertical cordon system with 6 rows. Rows are 4-5 ft. apart on center (red arrows). Plants are 12 to 18 in. apart within rows (green arrows). A 30 ft. X 96 ft. greenhouse would accommodate 528 to 570 plants.
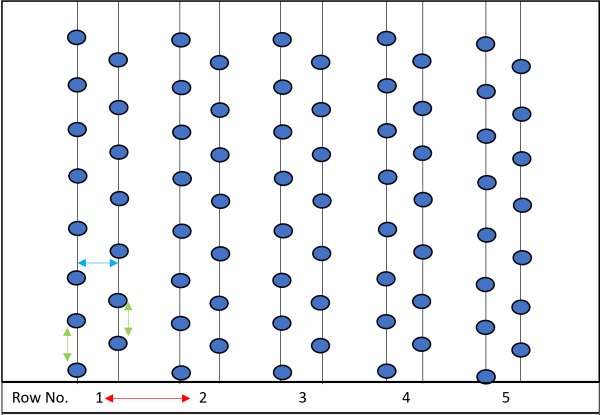
Figure 5. Double-row vertical cordon system with 5 rows. Wires are 24 in. apart within row (blue arrows). Rows are 5-6 ft. apart on center (red arrows). Plants are 18-24 in. apart within rows (green arrows) and staggered between wires to maximize light interception. A 30 ft. X96 ft. greenhouse would accommodate 440 to 570 plants.
The V-cordon system involves double-rows where plants are positioned between two wire cables. In the double- row system, the wire cables are spaced approximately 30 inches apart, and plants are trained on strings alternating between cables moving down the row. This arrangement creates a “V” effect, lending to the name V-cordon system (figure 6). The V-cordon allows for higher planting density with plants spaced 12′′ apart.
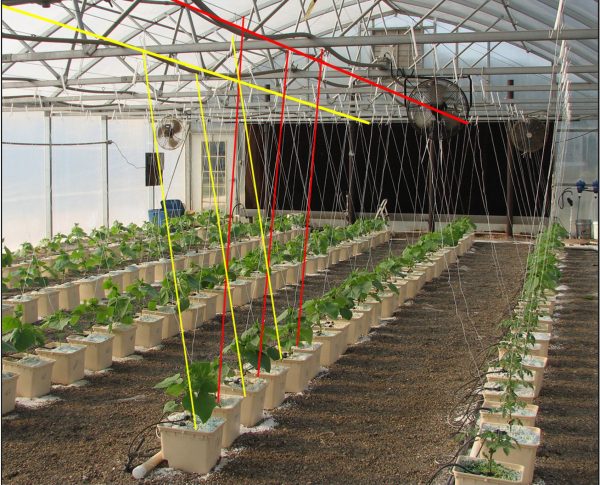
Figure 6. V-cordon training using the dutch bucket system. Wires are 30 in. apart within row. Rows are 5-6 ft. apart on center. Plants are 12 to 16 in. apart within rows and are centered between wires. Cordons are trained in a staggered between wires alternative between wires (yellow and red). A 30 ft. X 96 ft. greenhouse would accommodate 330 to 570 plants.
Several different pruning systems are available for cucumber production. The “umbrella system” and several variations have been widely used. These variations are typically associated with the presence or absence of side shoots. In some versions, several nodes are allowed to set fruit before being pruned. A simplified version, called “the modified umbrella system,” has become popular where no side shoots are allowed to form. Cordons are only single leaders. All systems involve clipping the growing point when the vine reaches the trellis cable. Two leaders are allowed to form and then trained in opposite directions horizontally on the cable for approximately 6′′ and then to drape back down toward the ground. During the training process, fruit is not allowed to form on the bottom 30′′ of the main cordon (figure 7). The umbrella system can be used with vertical or V-cordon training methods.
University of Florida research in the mid-1990s demonstrated increased yields with a method that left the terminal growing point intact. In this system, the vine is allowed to grow to the trellis, where it is trained to loop over the cable and drape back down as it continues to grow (figure 7). This led to a number of other international studies demonstrating similar results with training systems that kept the apical bud intact. Other variations include a lowering and leaning method similar to tomatoes and a method involving coiling the vine around the growing container as the cordon is lowered. In all cases, removing the growing point caused a delay in fruiting and subsequently led to a lower yield when compared to intact growing point methods. Intact growing point methods increased yields over umbrella- type methods from 7 percent to 43 percent across a number of studies.
The Greenhouse Environment
Cucumbers grow best at temperatures of 80 to 85 degrees F. Prolonged periods of temperatures above degrees F decrease the productivity and yield of cucumber plants. This is a frequent occurrence in greenhouses in the southeastern United States, especially during the summer months. Though greenhouse production is generally considered a year-round enterprise—and certainly can be in other regions—there is a seasonality when it comes to growing certain plants in the southeast, and cucumbers are typically grown as fall and spring crops in the greenhouse.
As temperatures get warmer in the greenhouse, it may be economically viable to use cooling strategies. Using a 50 percent shade cloth during warmer months limits the amount of heat entering the greenhouse. Still, it also reduces the light that reaches the plant, resulting in a longer production time to achieve marketable fruit. Evaporative cooling, which uses moisture to trap heat, is a common cooling method but has a limited cooling capacity in the south because of the region’s high humidity. Find more information on evaporative cooling on the Alabama Extension website, www.aces.edu. Temperatures below 65 degrees F will also decrease the growth and yield of cucumber plants.
Humidity is another important environmental factor that influences crop growth. Cucumbers grow well in high humidity (60 percent to 70 percent). Above this range, increased disease pressure can negatively affect crop yield. Provide adequate air movement throughout the growing environment to prevent pockets of high humidity.
Fertilization and Irrigation
Compared to leafy green production, cucumbers require higher levels of nutrients for fruit development, but nitrogen and potassium are essential (table 1.). Electrical conductivity (EC) and pH should be maintained at 2.0 to 2.5 mhos and 5.5 to 6.5, respectively. Growers have the option to mix their own fertilizer; however, the cost savings may not outweigh the convenience and reduced risk of using a preformulated hydroponic fertilizer. Cucumbers typically are fertilized with 150 to 200 ppm N solutions. Table 2 provides fertilizer rate and scheduling recommendations.
Fertilizer solution is supplied to cucumber plants grown in substrate through a drip irrigation line fitted with drip emitters that release a nutrient solution to the plant at a predetermined rate. A general rule of thumb is to supply enough water throughout the day to fully saturate the growing medium and provide 10 percent to 25 percent leachate from the pot. The irrigation rate will depend on the growth stage of the crop (smaller plants require less water) and the season (warmer temperatures require more irrigation). A 30 x 96 foot greenhouse can require 500 to 1,000 gallons of water per day.
Table 1. General Recommendations for Nutrient Solution Concentrations
Adapted from Gnayem, N. “Recommendation on growing greenhouse Beit-Alpha cucumbers. Ministry of Agriculture- Israel.” (2006).
Crop Age | Concentration of N Reported in ppm | Concentration of P Reported in ppm | Concentration of K Reported in ppm | Concentration of Ca Reported in ppm | Concentration of Mg Reported in ppm |
---|---|---|---|---|---|
0–14 Days | 60–80 | 23–35 | 50–70 | 60–80 | 35–40 |
Flowering to Harvest | 100–120 | 25–30 | 140–160 | 80–100 | 35–40 |
After First Harvest | 120–140 | 30–40 | 160–180 | 80–100 | 35–40 |
Table 2. Sufficiency Ranges for Cucumber Tissue & Nutrient Concentrations
Adapted from Mills and Jones 1996 and from Papadopoulos 1994.
Macronutrients | Tissue Sufficiency Ranges | Nutrient Solution Concentration Ranges (ppm) |
---|---|---|
Nitrogen | 4.2%–5.8% | 150–200 |
Phosphorus | 0.58%–1% | 50 |
Potassium | 3.33%–4.56% | 300–500 |
Calcium | 2%–2.5% | 150–300 |
Magnesium | 0.4%–0.71% | 50 |
Sulfur | 0.32%–0.63% | 50–200 |
Iron | 65–300 ppm | 6 |
Manganese | 55–300 ppm | 1 |
Boron | 50–60 ppm | 0.3–0.5 |
Copper | 5–17 ppm | 0.1 |
Zinc | 52–140 ppm | 0.5 |
Molybdenum | 1–2 ppm | 0.05 |
Harvesting and Fruit Quality
Fruit should not be left on the plant once it reaches a marketable size. Overripe fruit can taste bitter and decrease its marketability. Misshapen fruit can occur in greenhouse settings for several reasons. Prune this fruit as you see it so the plant can put resources toward growing marketable fruit. Crooking and curling can occur for several reasons, some of which interact. A lack of water can cause fruit to become deformed, and this can be enhanced when essential plant nutrients such as potassium are insufficient. Sometimes fruit can get caught on or between objects such as vine clips or training wires, affecting its growth.
At optimum light levels (DLI 30 or greater), it takes cucumbers 10 days from fruit set to marketable fruit. The time from fruit set to harvest will increase with lower light levels. Cucumbers produce multiple fruits per plant; therefore, growers should harvest numerous times per week to ensure that the fruit does not overmature on the plant. Daily harvest is needed to maintain a specific size. It is common to get 20 to 25 pounds of cucumbers per plant over a 12-week harvesting period for the spring crop. Harvest fruit in the early morning when it is cool and before the plants become heat stressed.
Cucumbers are often peeled because of the thick skin surrounding the fruit; however, the “seedless” types can forgo the peeling process due to their thin skin. The disadvantage of thin skin is a faster rate of moisture loss, thereby reducing the post-harvest quality. Seedless cucumbers are wrapped in plastic to reduce moisture loss and maintain crispness. In the case of the English types, each fruit is individually wrapped because these fruits reach 12 to 14 inches in length (300 to 400 grams). The Beit-Alpha types are much smaller and are typically harvested between 6 and 8 inches in length (80 to 120 grams) and are often packaged in cellophane-wrapped foam butcher trays with typically 5 to 7 fruit per tray (figure 8).
Cucumbers can be stored up to 14 days post harvest at 50 degrees F. Beit-Alpha cucumber fruit can be stored safely at 45.5 degrees F for 7 days.
Suggested Reading and Literature Cited:
- Gnayem, N. “Recommendation on growing greenhouse Beit-Alpha cucumbers. Ministry of Agriculture-Israel.” (2006).
- Hochmuth, R. C., L. Lani, L. Davis, W. L. Laughlin, E.H. Simonne, S.A. Sargent and A. Berry. (2004). Evaluation of twelve greenhouse Beit-Alpha cucumber varieties and two growing systems. Acta. Hort. 659:461–466.
- Mills, H. A. and Jones Jr., J. B. (1996) Plant Analysis Handbook II. A Practical Sampling, Preparation, Analysis, and Interpretation Guide. Micro-Macro Publishing, Athens.
- Papadopoulos, A. P. (1994). Growing greenhouse seedless cucumbers in soil and soilless media. Agri. and Agri-Food Canada Publication 1902/E: Ottawa, Ontario.
- Resh, H.M. (2012). Hydroponic Food Production: A Definitive Guidebook for the Advanced Home Gardener and the Commercial Hydroponic Grower, Seventh Edition (7th ed.). CRC Press.
- Villalta, Alfredo M., et al. “Sensitivity of Beit Alpha cucumber (Cucumis sativus L.) to low temperature storage.” Proceedings of the Florida State Horticultural Society. Vol. 116. 2003.
Caroline Blanchard, Research Associate, Horticulture; Jeremy Pickens, Assistant Extension Professor, Commercial Horticulture; and Daniel Wells, Associate Professor, Horticulture, all with Auburn University
New September 2022, Greenhouse Cucumber Production, ANR-2926